Introduction
In the rapidly evolving world of 3D printing, one company stands out with its innovative approach and cutting-edge technology. Glück, a Korean 3D printing company, has made a name for itself in the industry with its groundbreaking product, Sculpia, designed specifically for humanoid parts.
Our BOT investigator (Victoria) has been traveling Portugal, Korea, and soon Seattle to visit companies that are doing groundwork operations in the realm of humanoids.
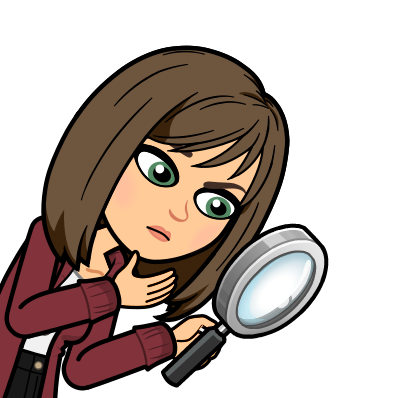
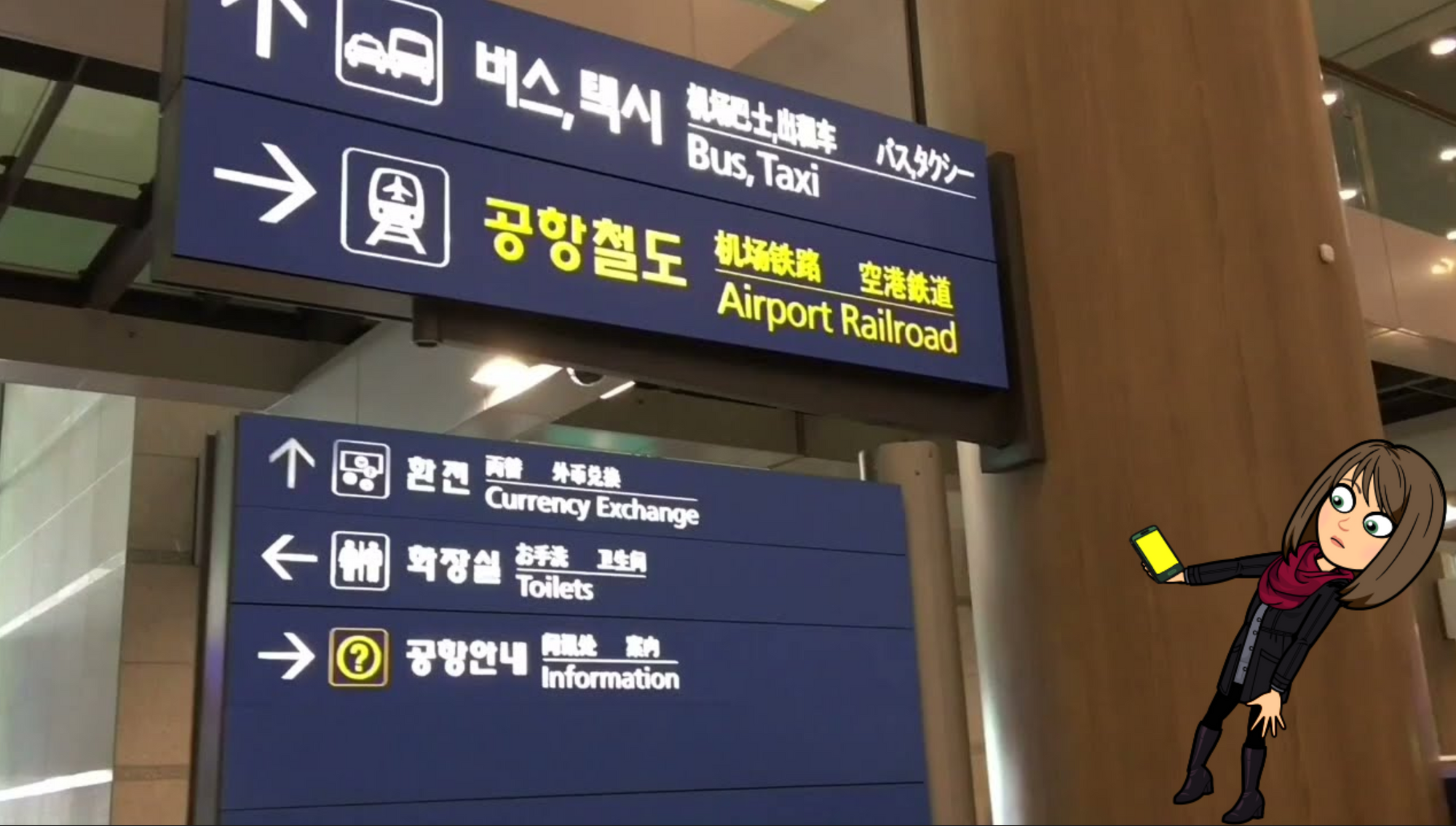
Glück and Its Vision
Glück is not just a company; it's a vision for the future of additive manufacturing. With a focus on creating high-quality 3D-printed humanoid components, Glück is pushing the boundaries of what's possible in the realm of 3D printing. The company's commitment to innovation and quality has made it a leader in the Korean 3D printing industry.
Sculpia is Glück's flagship product, a testament to the company's innovative spirit and technical prowess. Designed for humanoid parts, Sculpia is revolutionizing the way we think about 3D printing and robotics. The humanoid robots were created for an installation at local designer eyewear brand Gentle Monster’s Nudayk Store in Hanam, simulating a robotic assembly line.
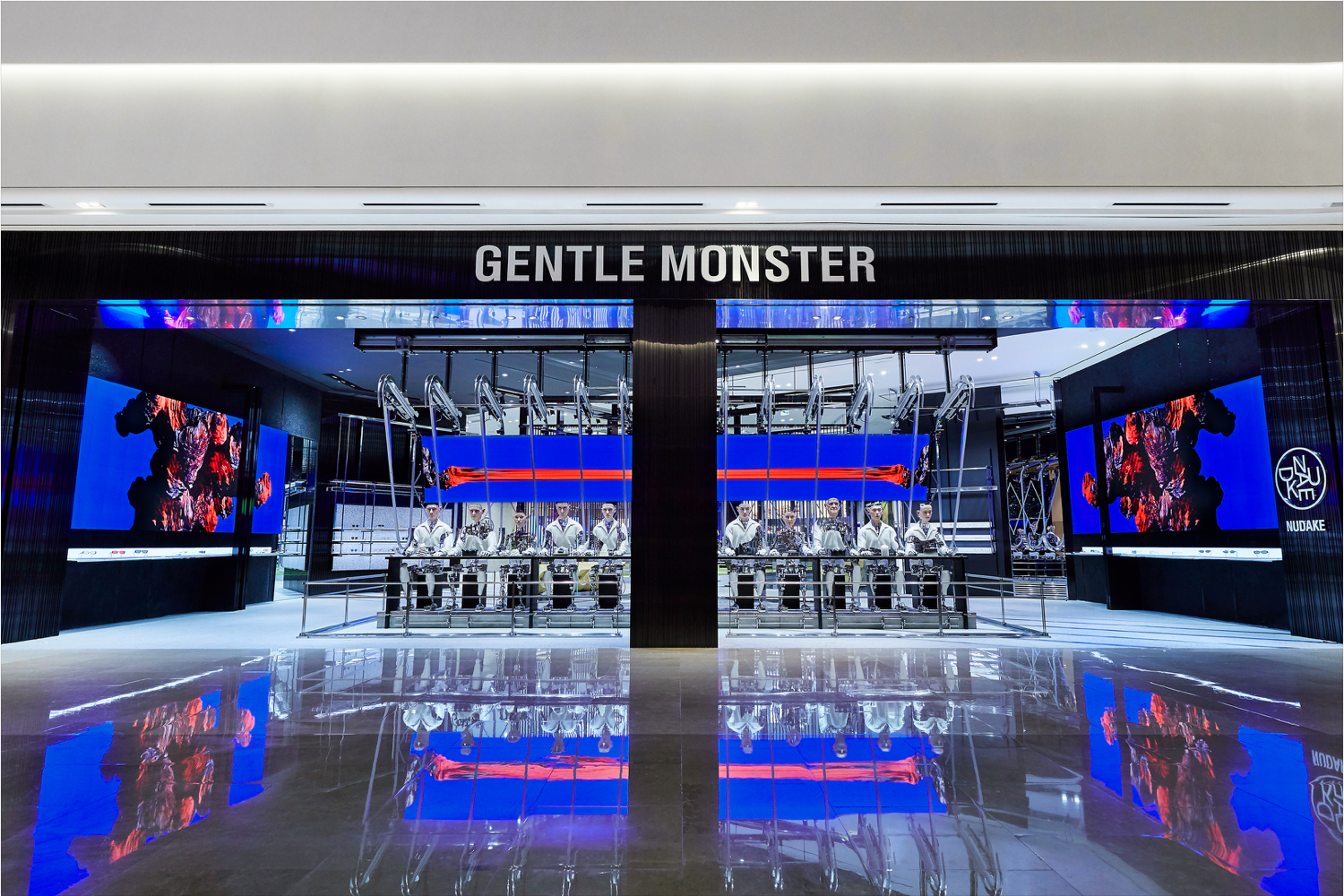
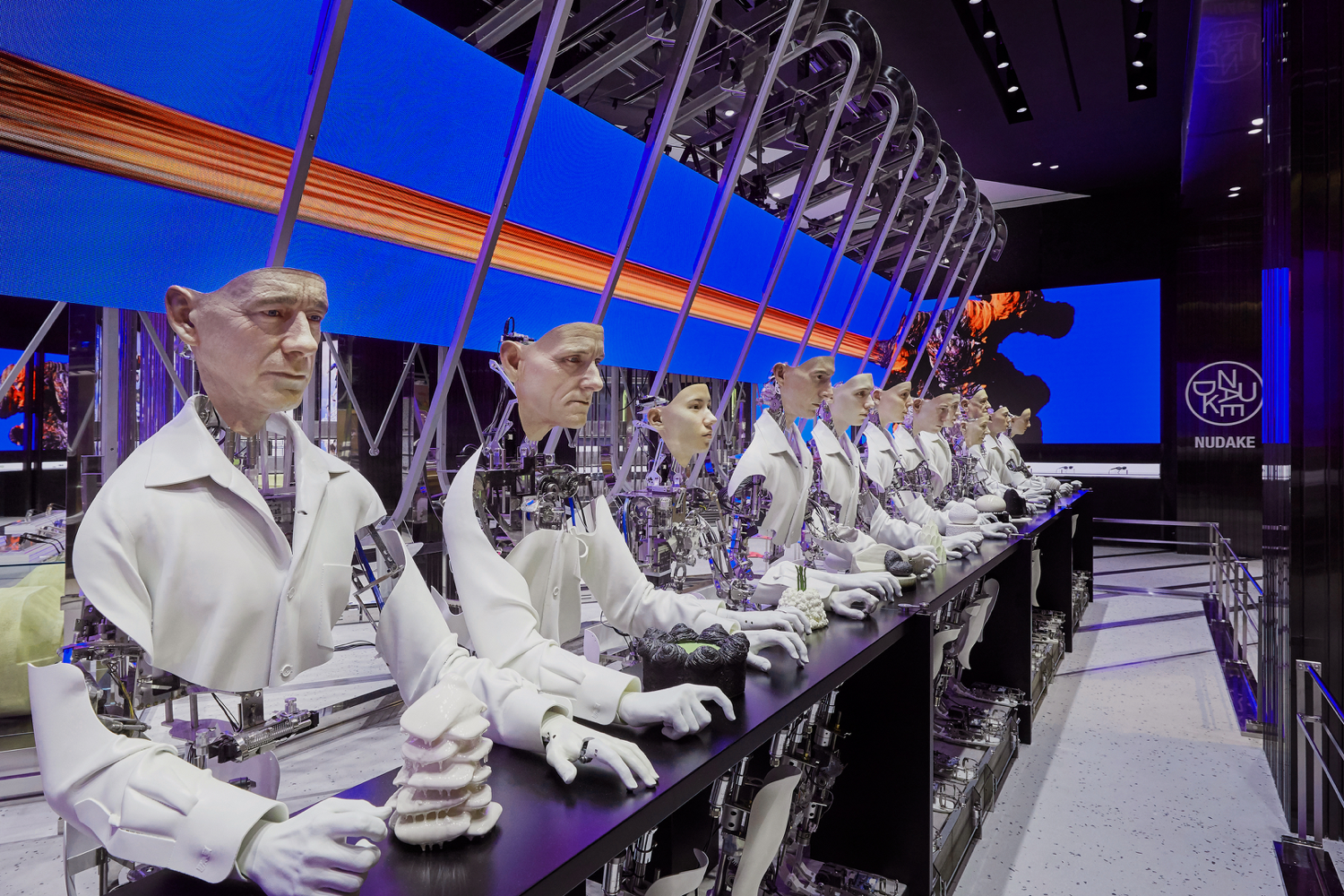
The Technology Behind Sculpia
Sculpia leverages advanced 3D printing technologies such as Fused Deposition Modeling (FDM), Stereolithography (SLA), and Selective Laser Sintering (SLS). These technologies, combined with Glück's proprietary techniques, result in humanoid parts that are not only structurally sound but also aesthetically pleasing.
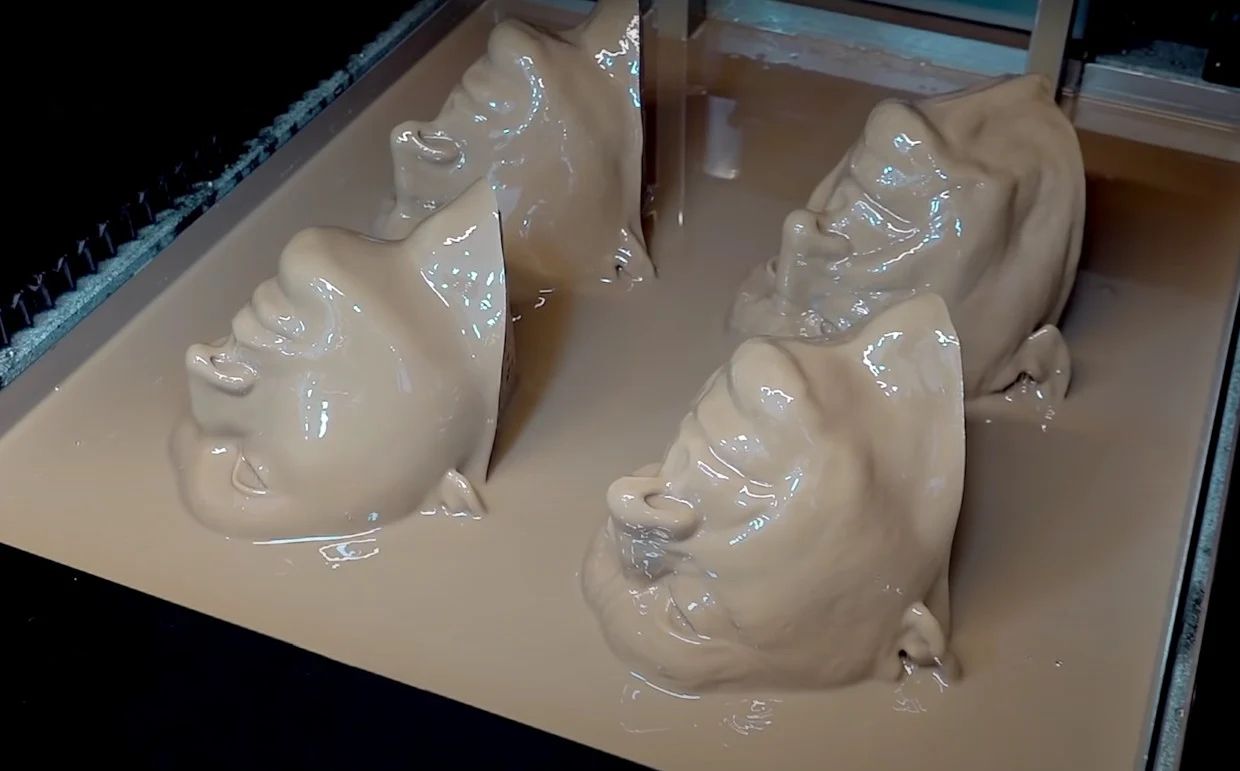
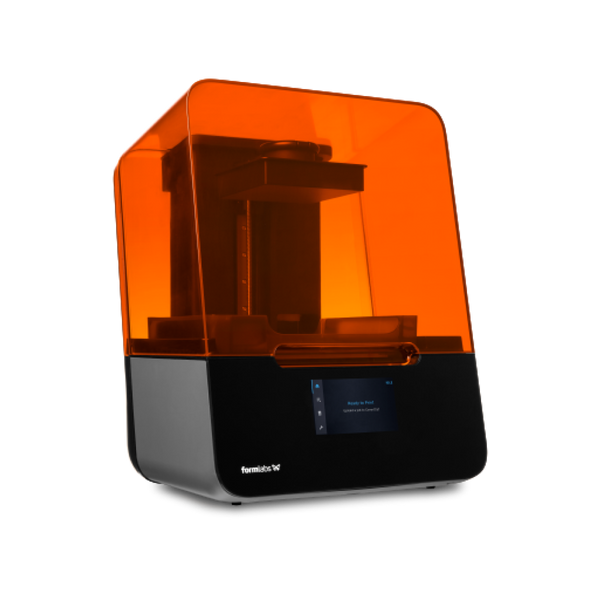
Form 3+
Each Form 3+ Low Force Stereolithography (LFS)™ 3D printer package produces functional, high-quality prototypes and end-use parts in record time with the Form 3+, an affordable, industrial-quality 3D printer that consistently delivers. The Form 3+ offers rapid print speeds, industry-leading accuracy and reliability, and a wide range of materials.
The Form 3+ is powered by Low Force Stereolithography which consistently delivers presentation ready parts with unbelievable surface finish. After printing, detach supports in seconds with our enhanced Light Touch Support structures that save post-processing time.
The Form 3+ is simple to set up and maintain. Use the Form 3+ for both prototyping and production and easily add more capacity as demand grows.
If you have never seen an SLA machine in real life, here is a shot for you that Victoria has taken on a recent visit to Korea. Thanks to our Korean subscribers for shuttling her around!
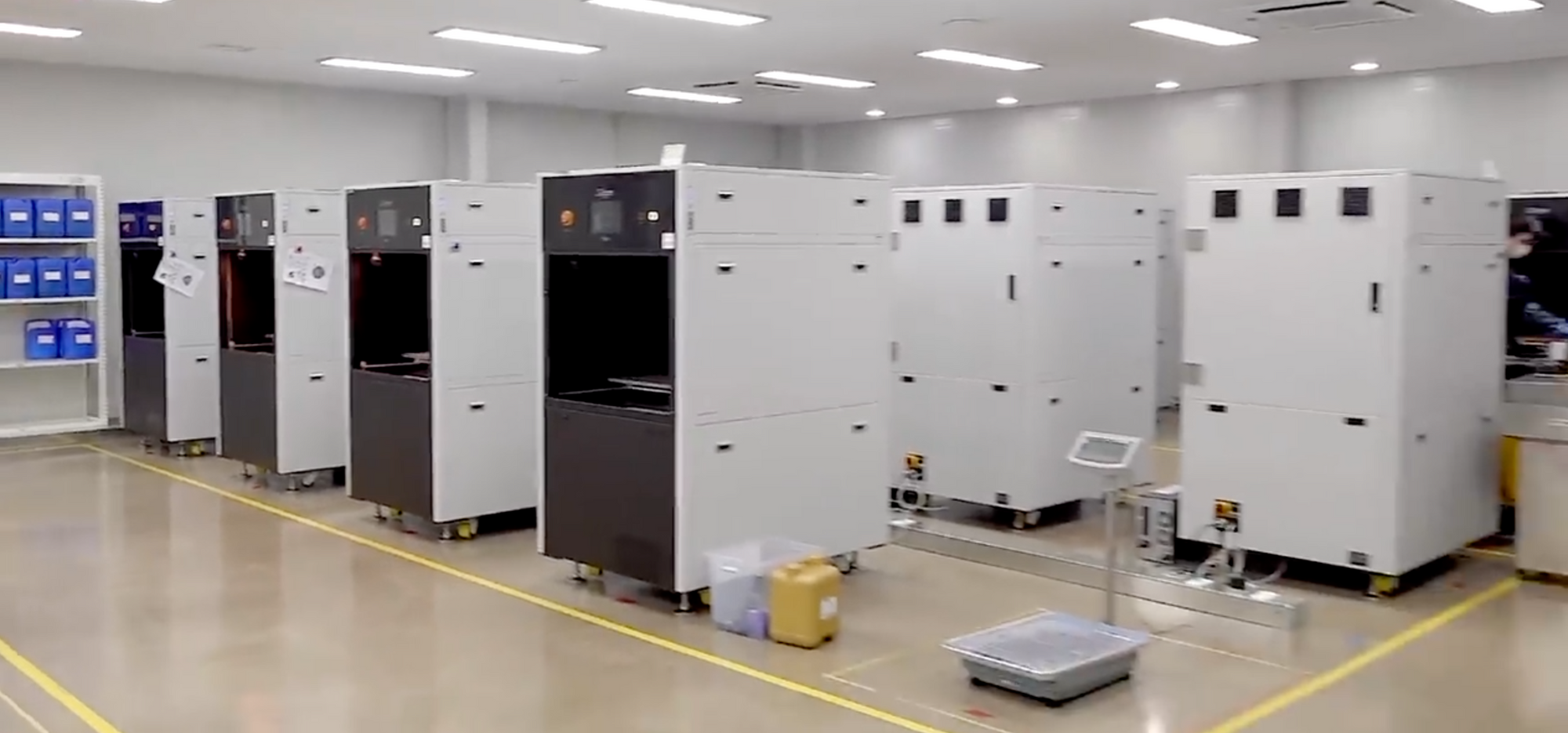
Glück's Industrial Impact
In 2021, Glück opened Korea’s largest industrial 3D printing automation factory, the Wico3D Printers facility, in Paju, Gyeonggi-do. The company introduced 16 MAX600 SLA systems from Cubicon with a short-term plan to mass-produce silicone molds and surgical simulators and a longer-term plan to add a metal 3D printing business. This move has solidified Glück's position as a leader in the industrial 3D printing sector.
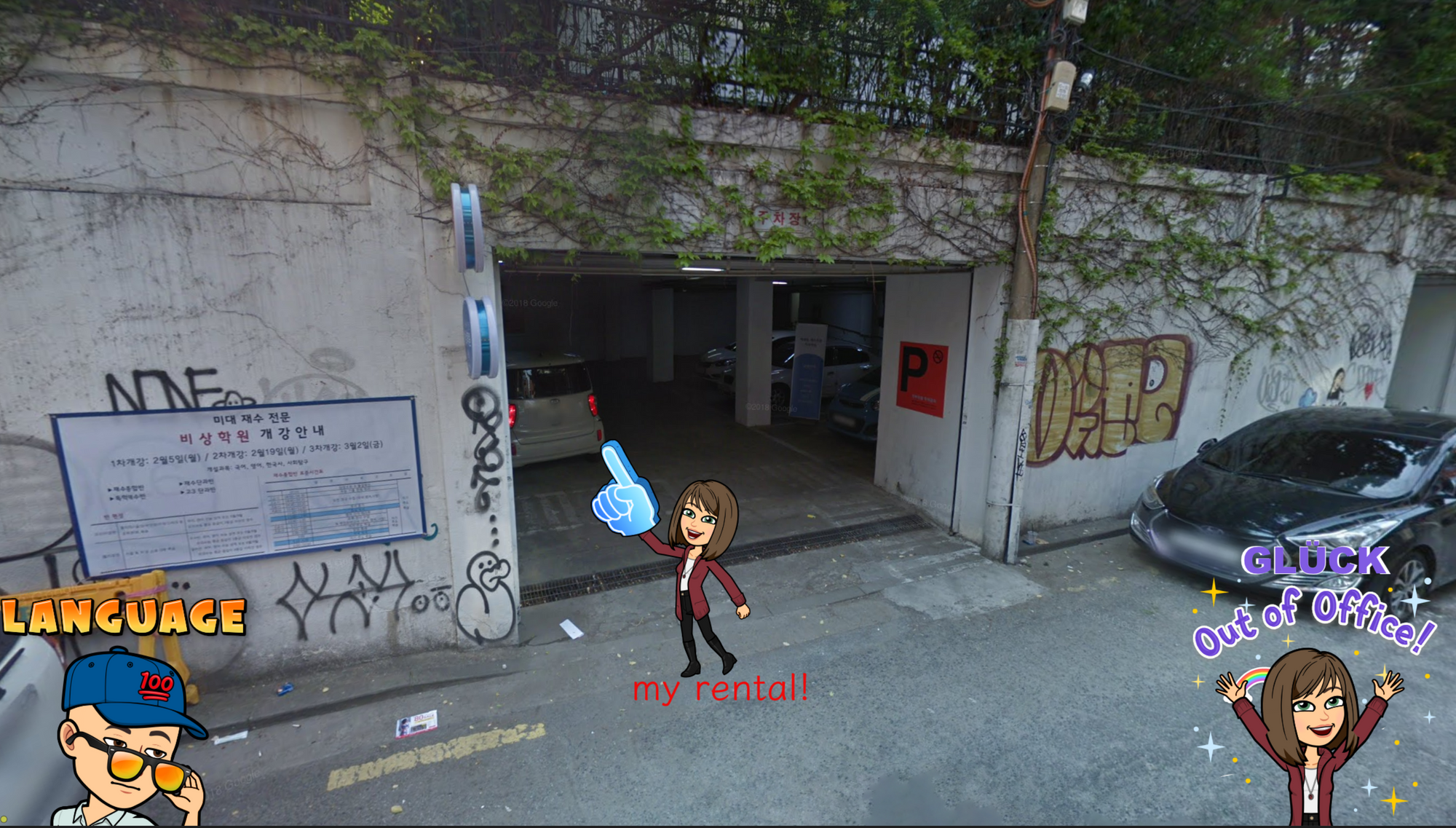
Glück's Contribution to the Maker Space
Glück has built up experience in the development of over 10,000 prototypes using 3D printing since 2013. The company is currently operating a specialized 3D printing lab through the maker space (the GLUCK 3D Printing Fab Lab), supporting professionals in the industrial and medical fields. This initiative has been instrumental in fostering innovation and promoting the use of 3D printing technology in various fields.
Let's dig in!
Well... not literally! Never mind, in the words of Hamilton: So...we are doing this! In the scenario of the printed heads, in the back of the shells, there's a supportive material that has to be removed and the counterpart cleaned.
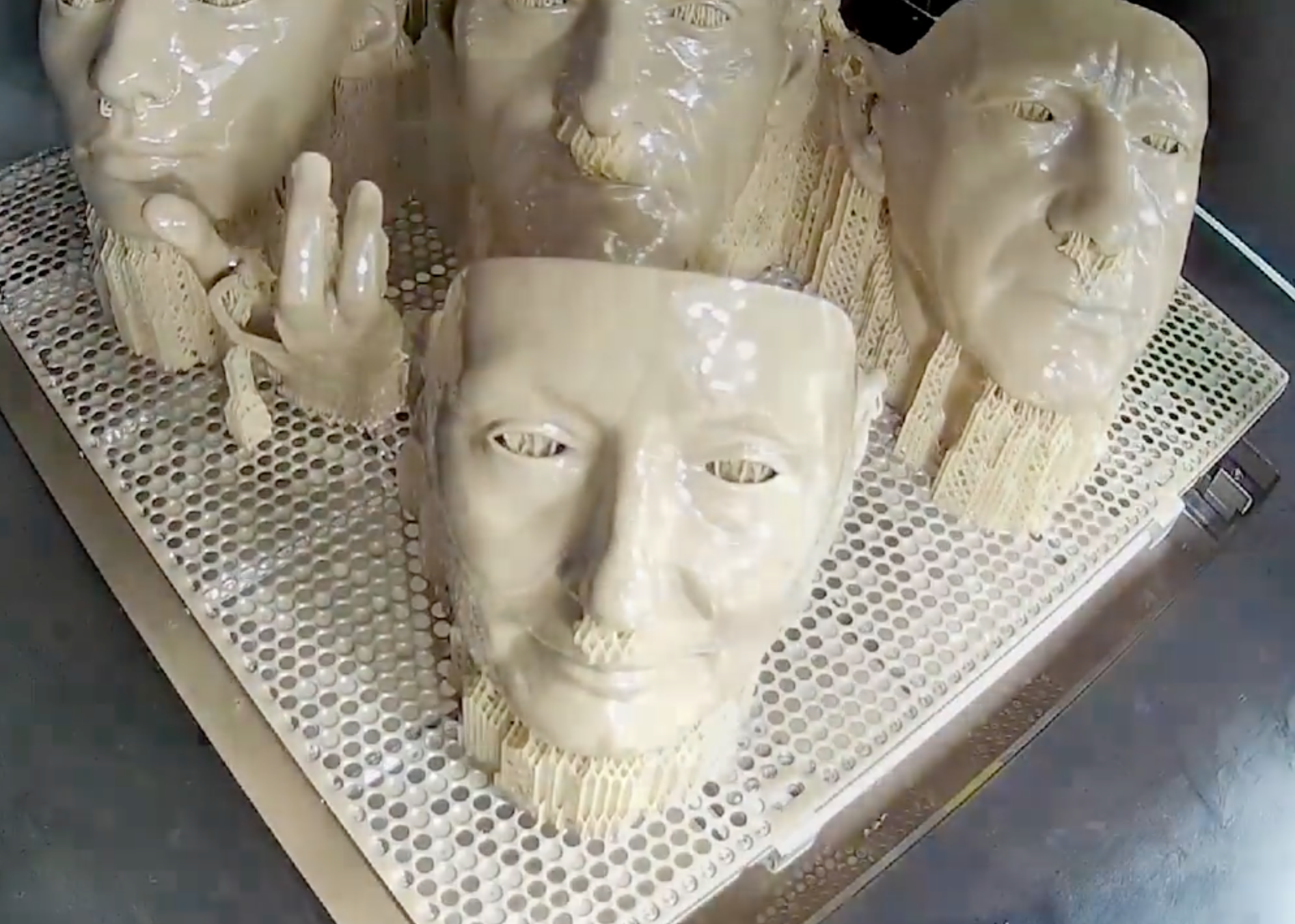
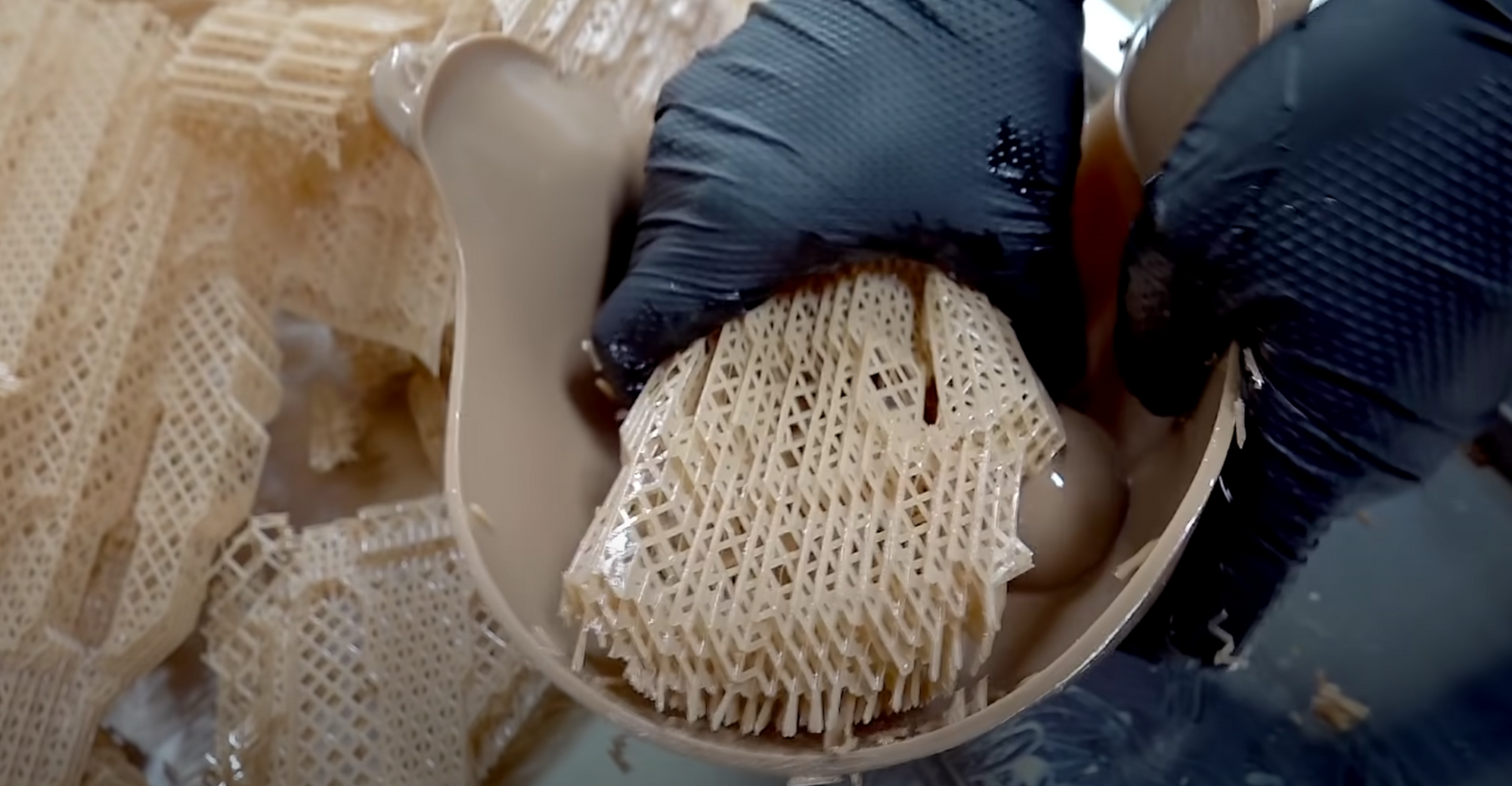
After the bulk cleaning (the support), they are transported to the cleaning station, which is basically a gigantic "dishwasher" to remove deposits, polish, and smooth.
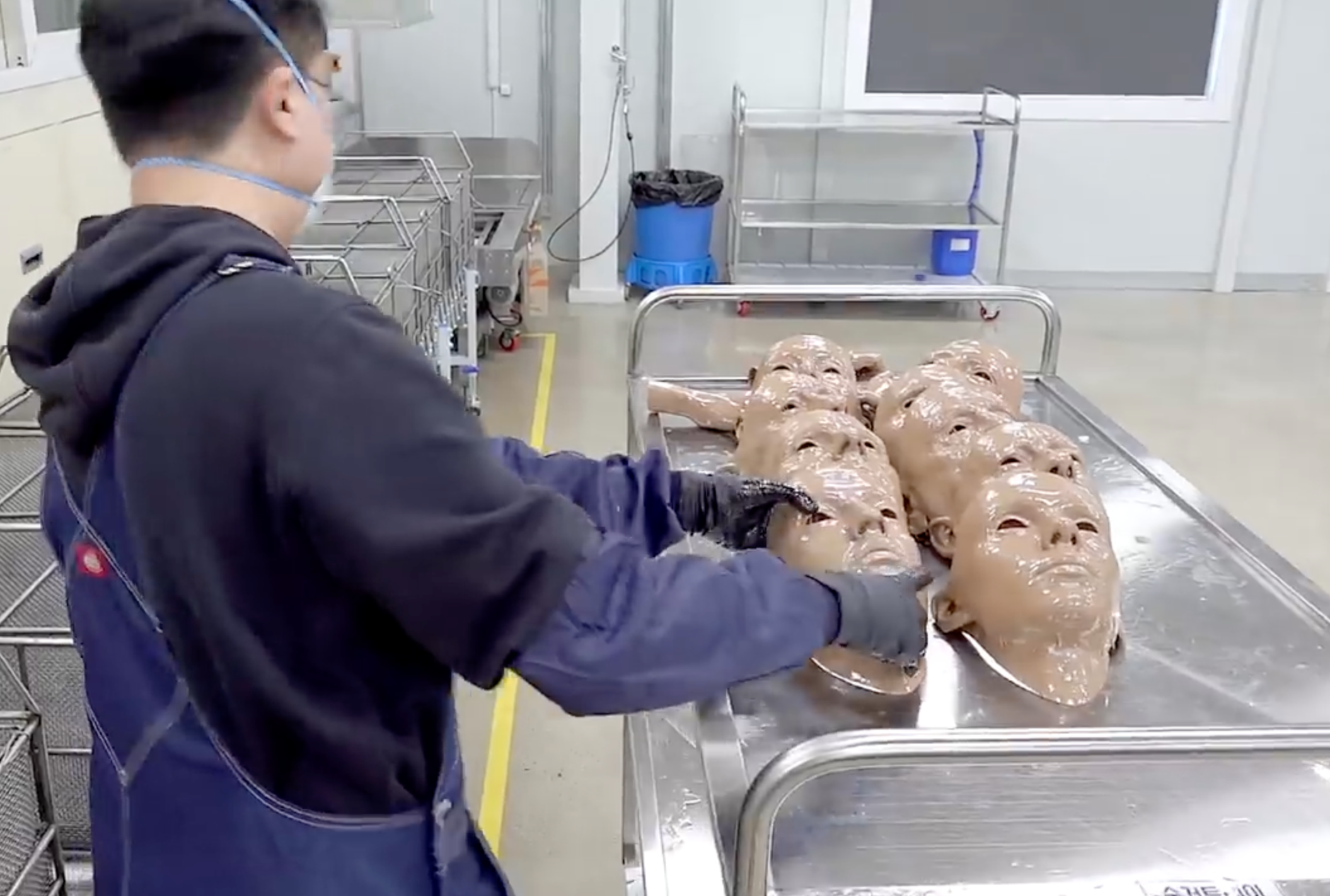
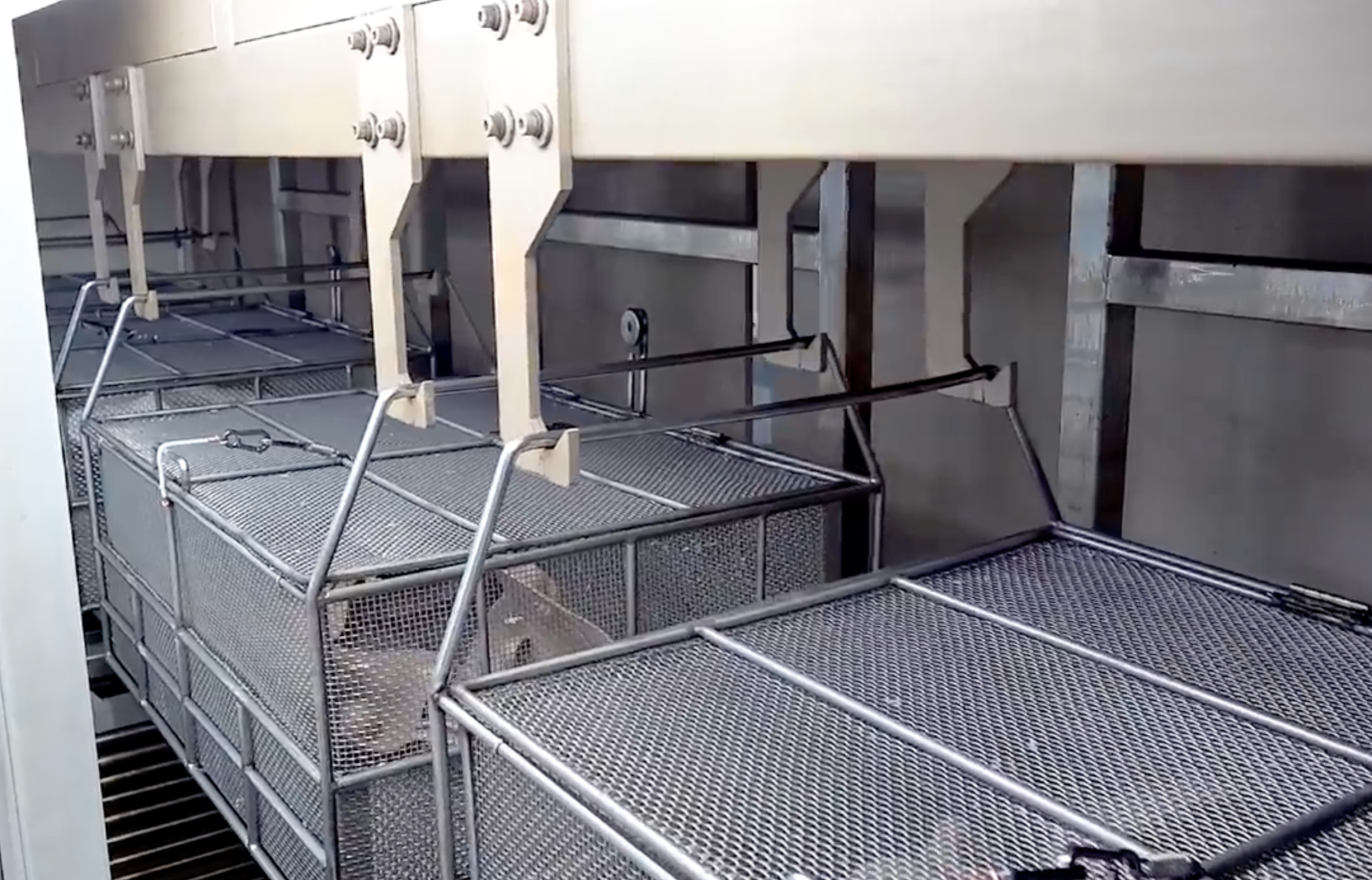
For some reason seeing those faces appearing from "nothing" didn't make any scary impression on me as much as when I saw the fingers showing up from the printers. It reminded me of the only book my Kindle had cached. I know not the most light reading... but it was either that or learning Korean from the airport to the destination (several hours).
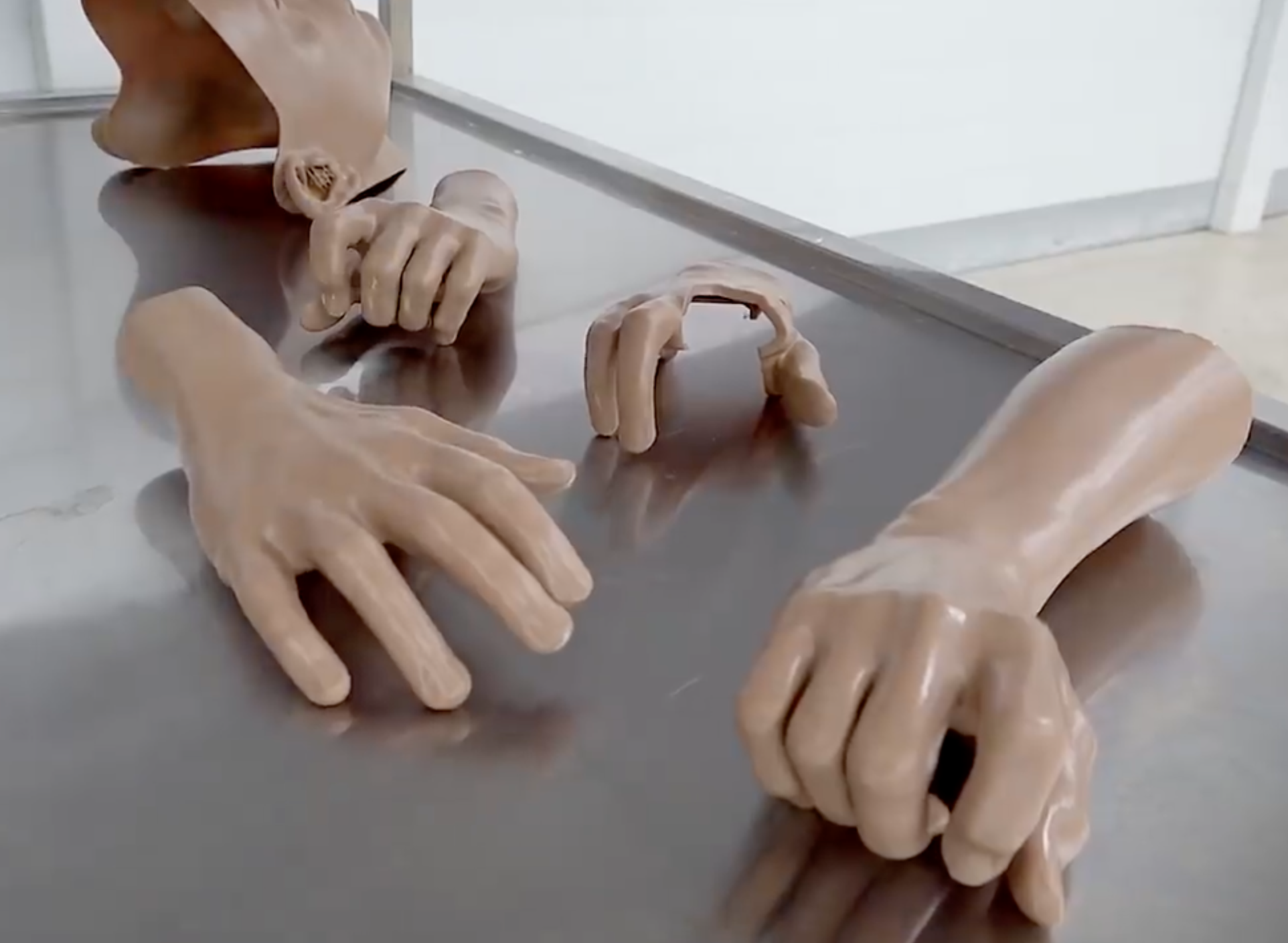
After the washing and rising phase, the parts are air pressured and moved into the UV curation chamber. To keep the kitchen appliances analogy going, this part of the process is the oven!
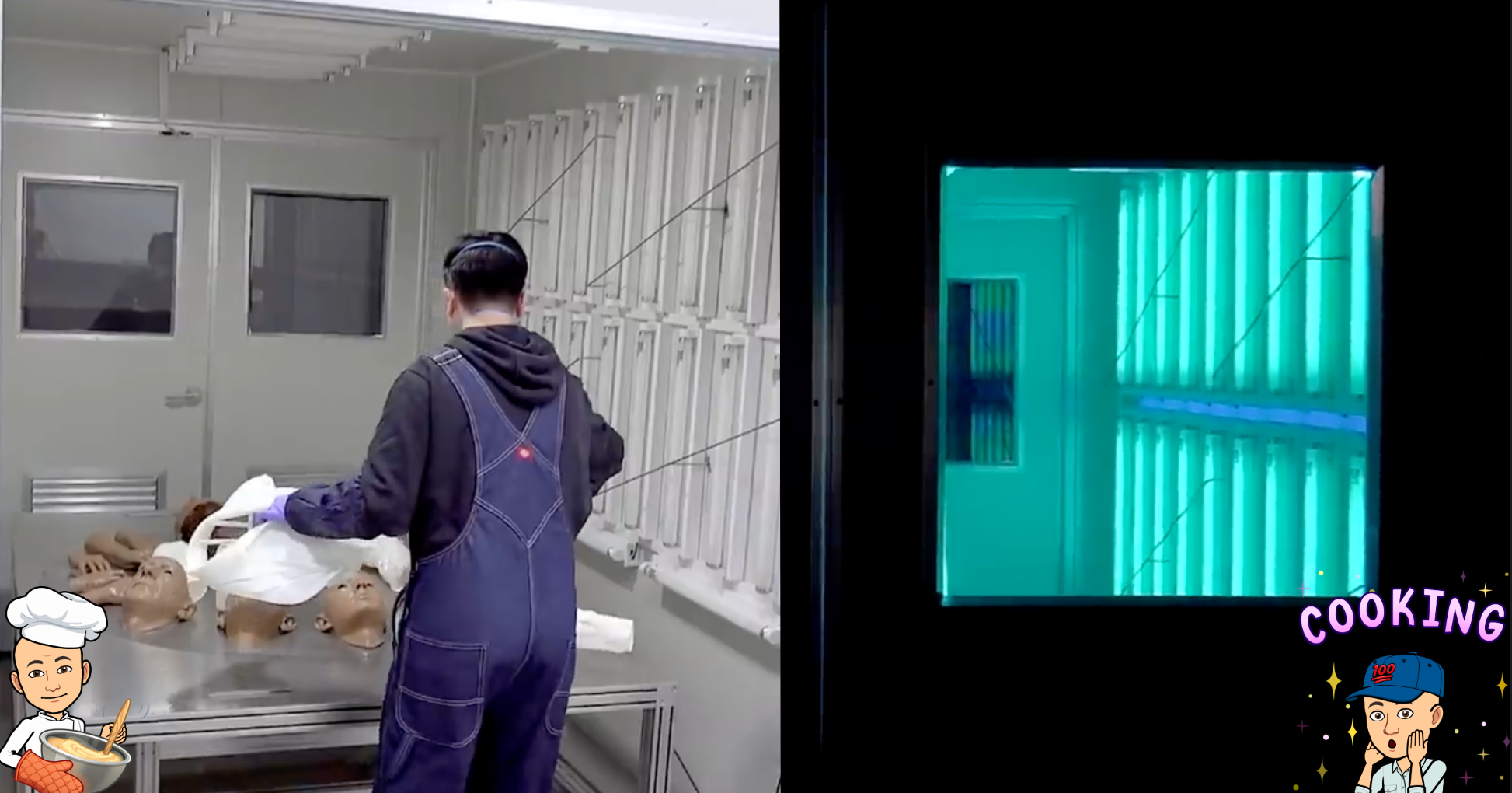
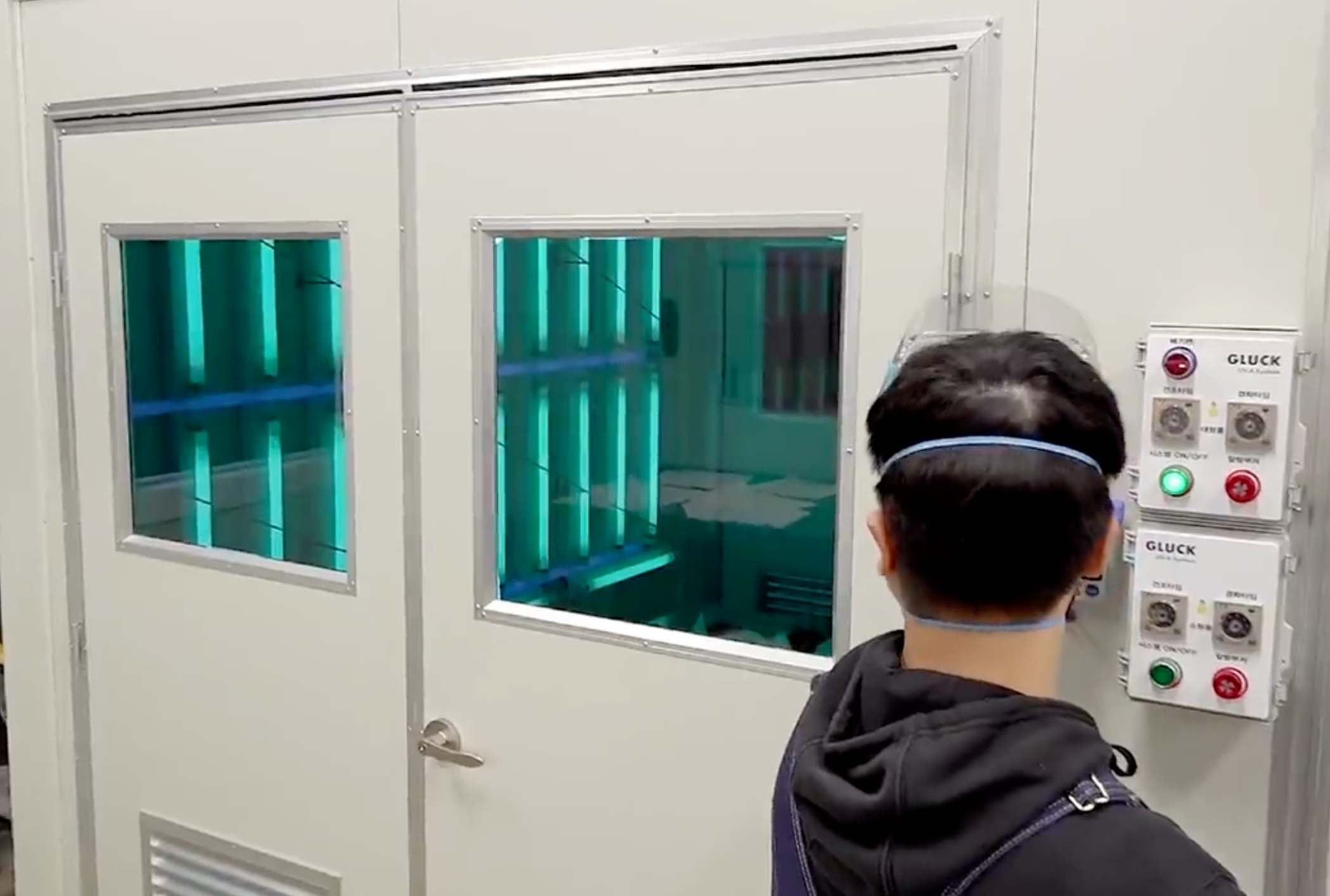
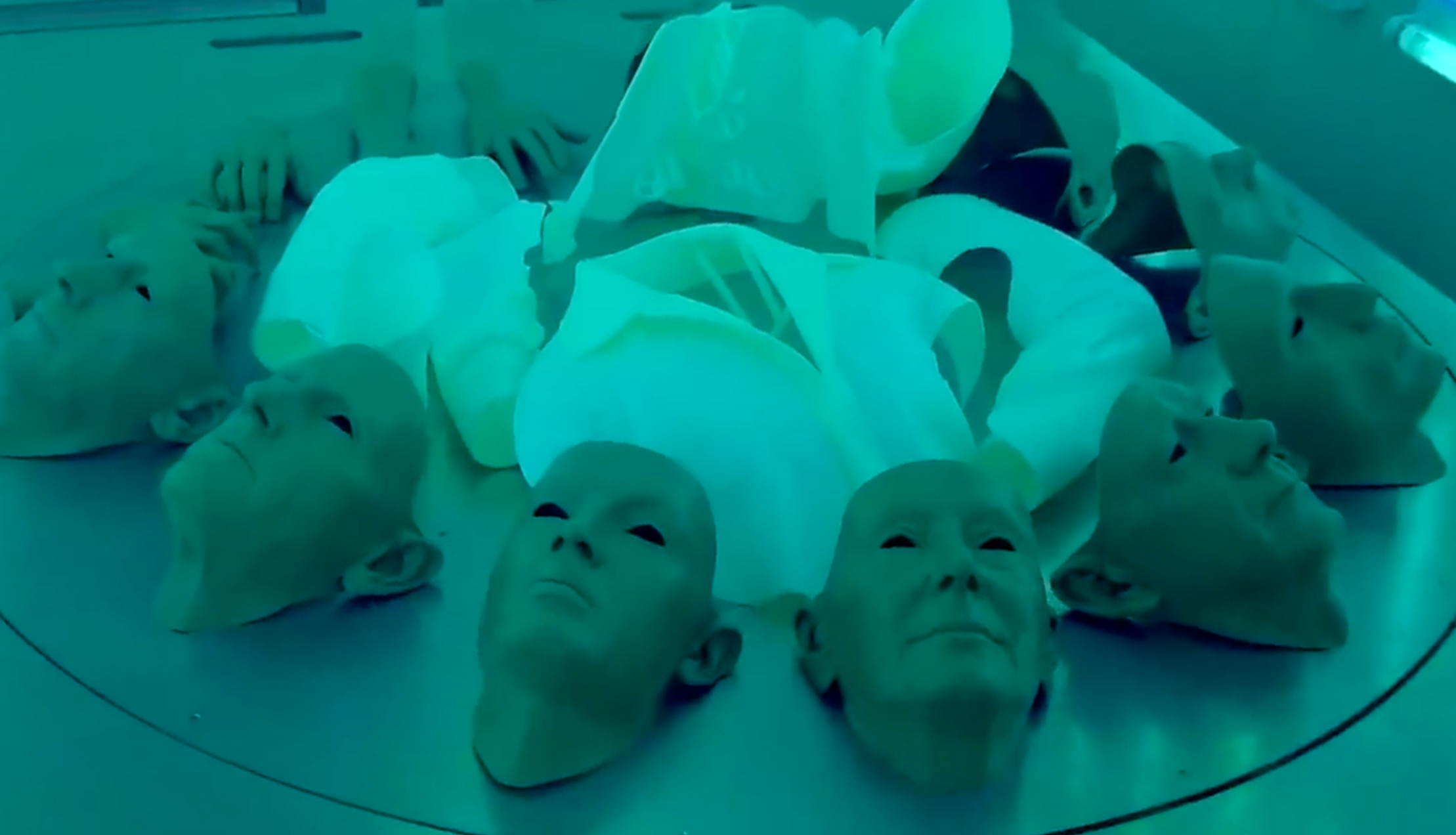
After this process, the "humanization" process of printing happened, and perhaps this was a display of Korean talent and dedication to details in manufacturing. It is hard to portray how coordinated the movements were in blasting the texture to give a less "plastic-y" look at the parts, in adding features, eyeballs, and all other human-like features to the prints.
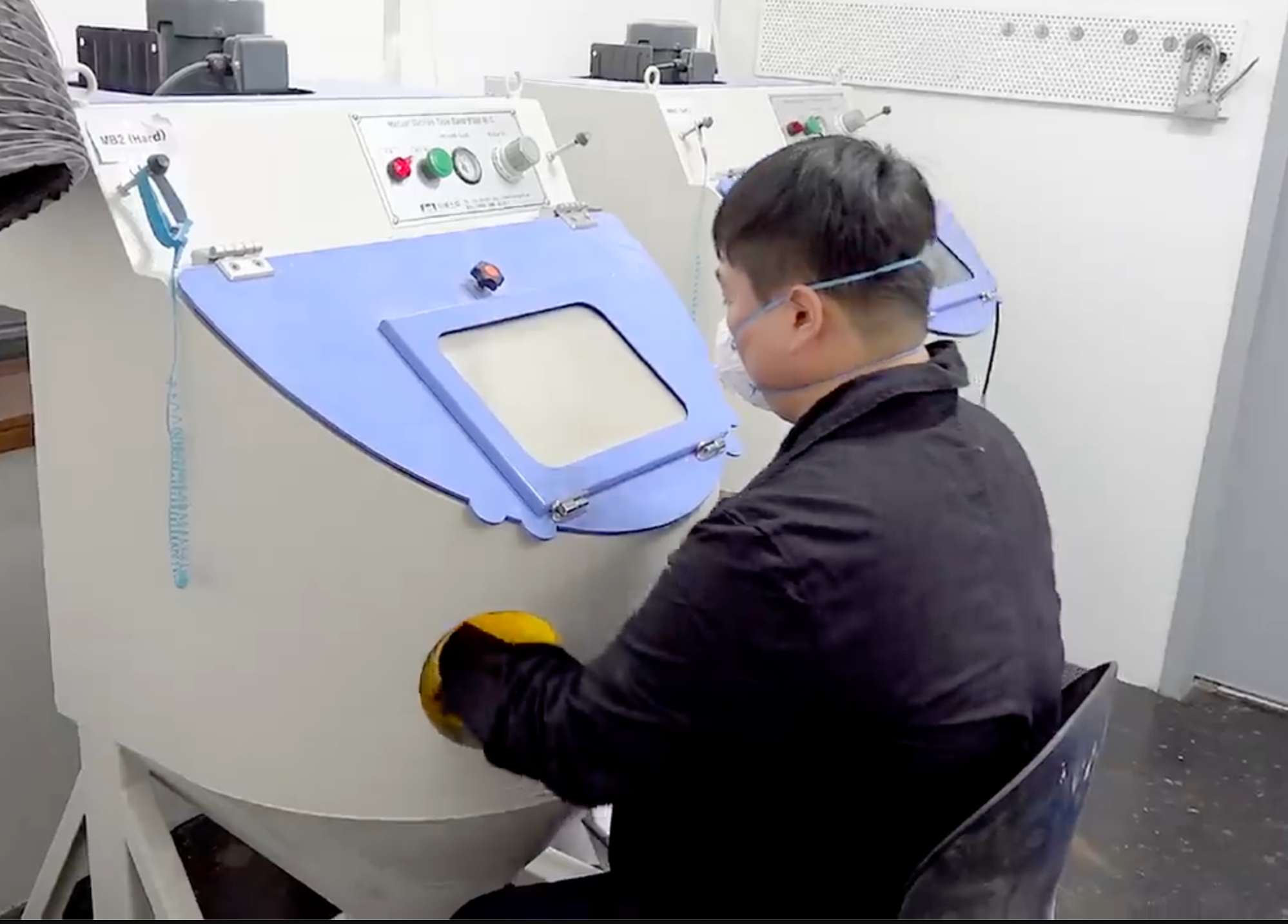
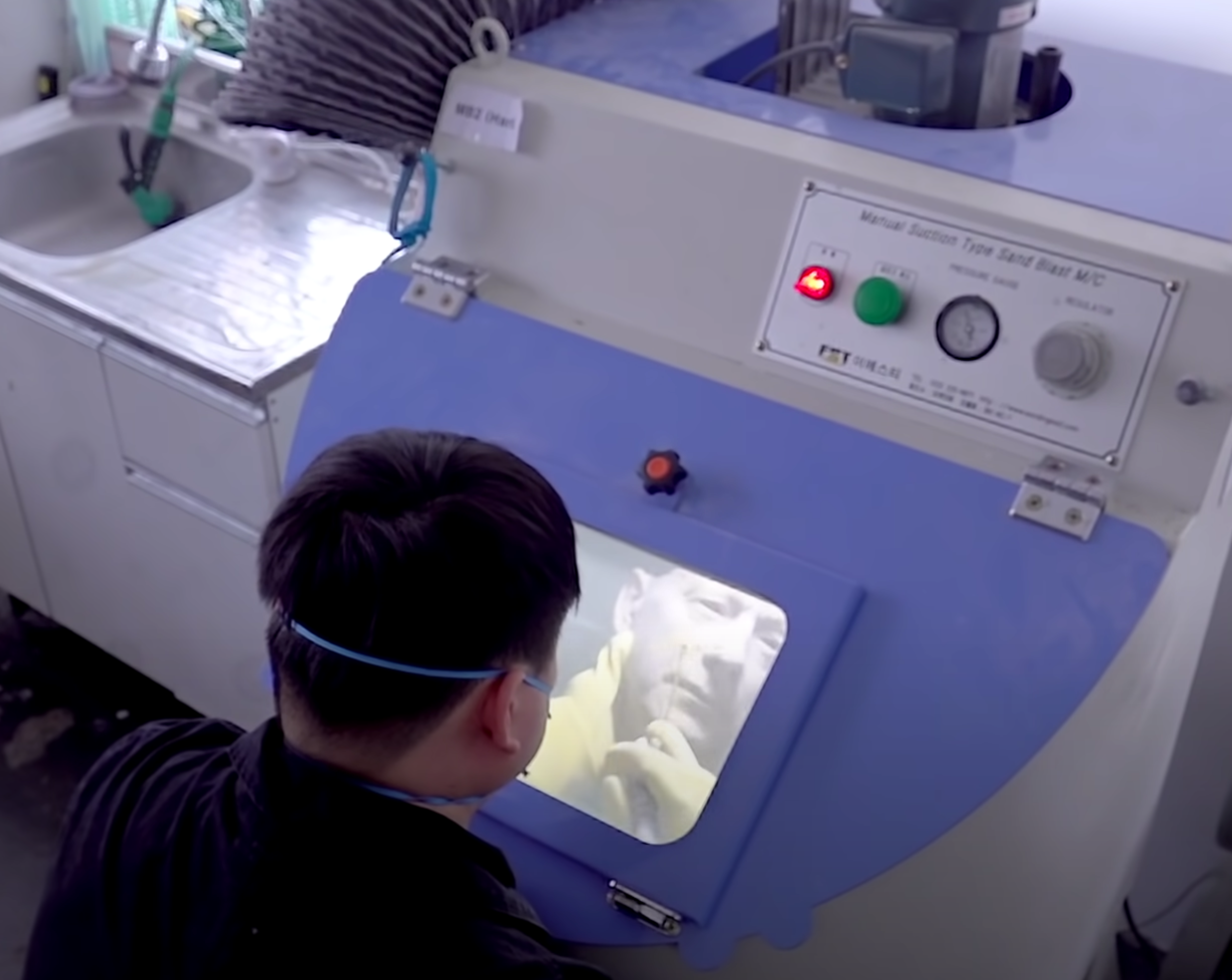
After the texture, the parts are moved to the details station, where an artist applies colors and features.
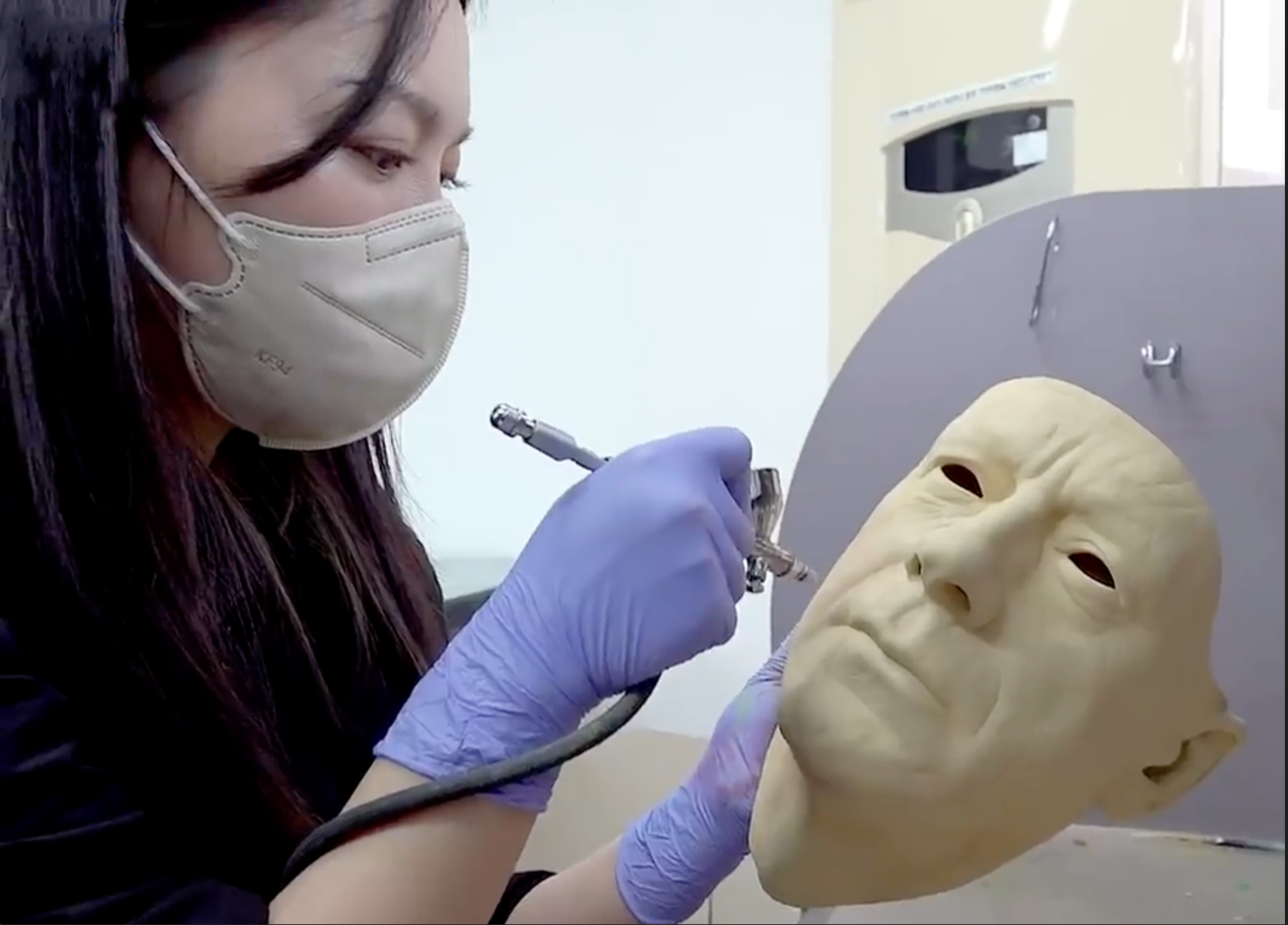
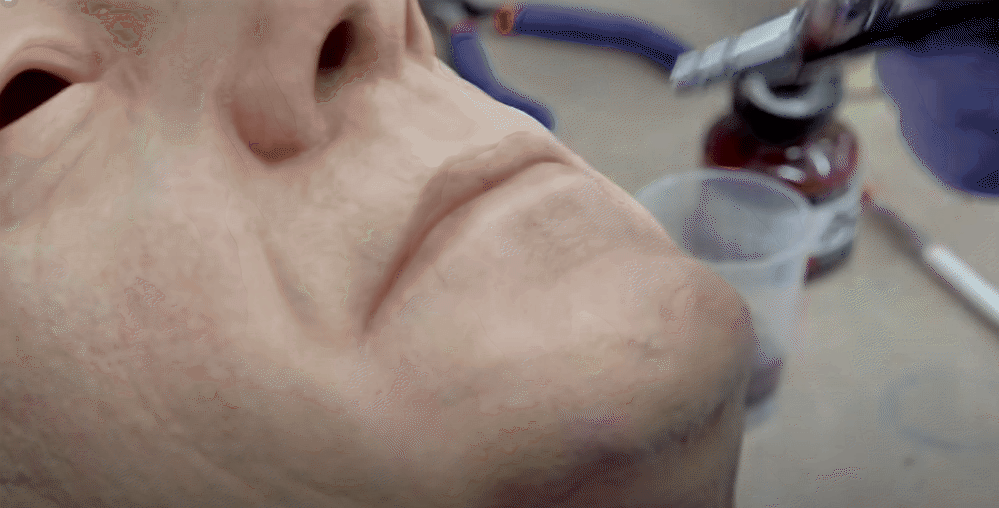
Not everything is done with machinery. For example, I wish I had the skills that Muyi (the artist) has displayed in making my own eyebrows—something to be speechless about.
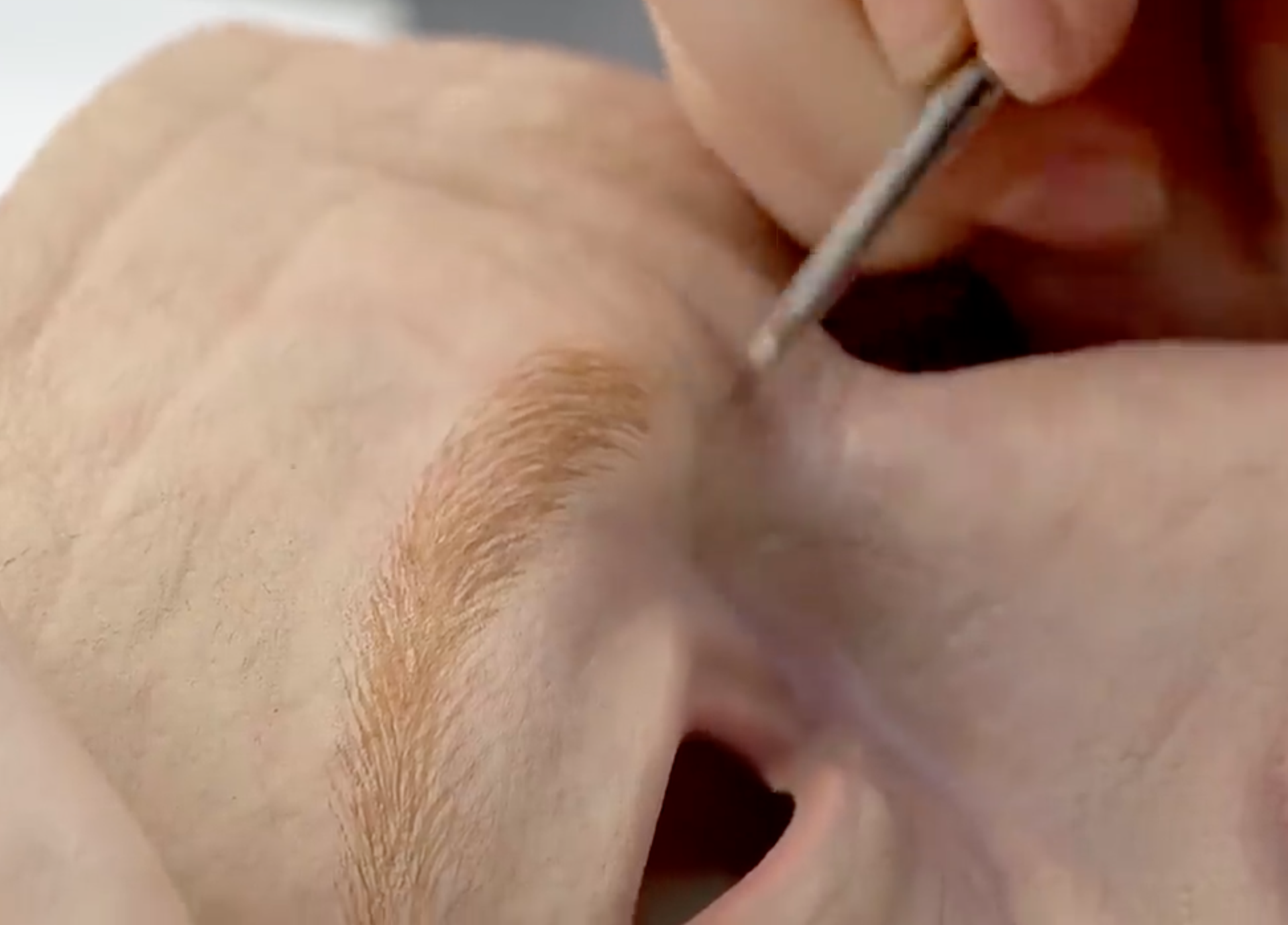
a few more touches, then after everything is settled, they are taken to the storage room for one day, and the next day, the mechanics that animate the parts are installed.
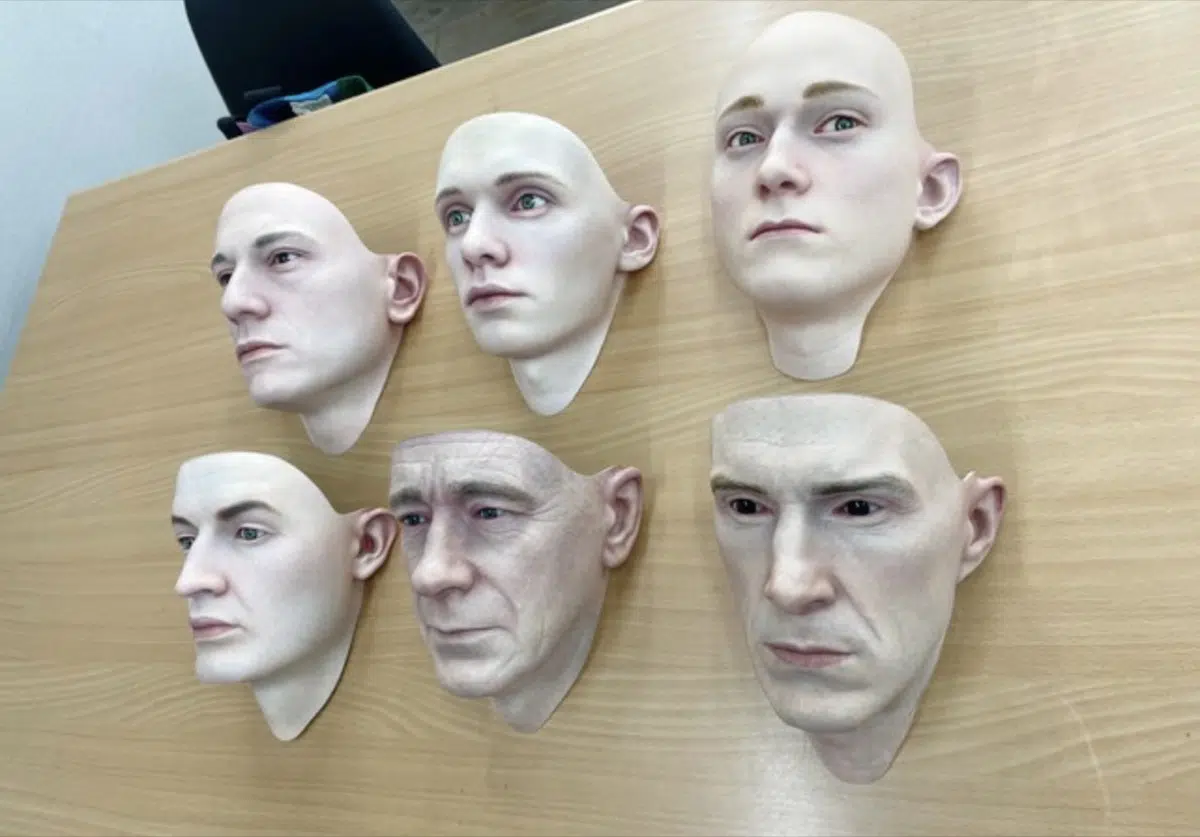
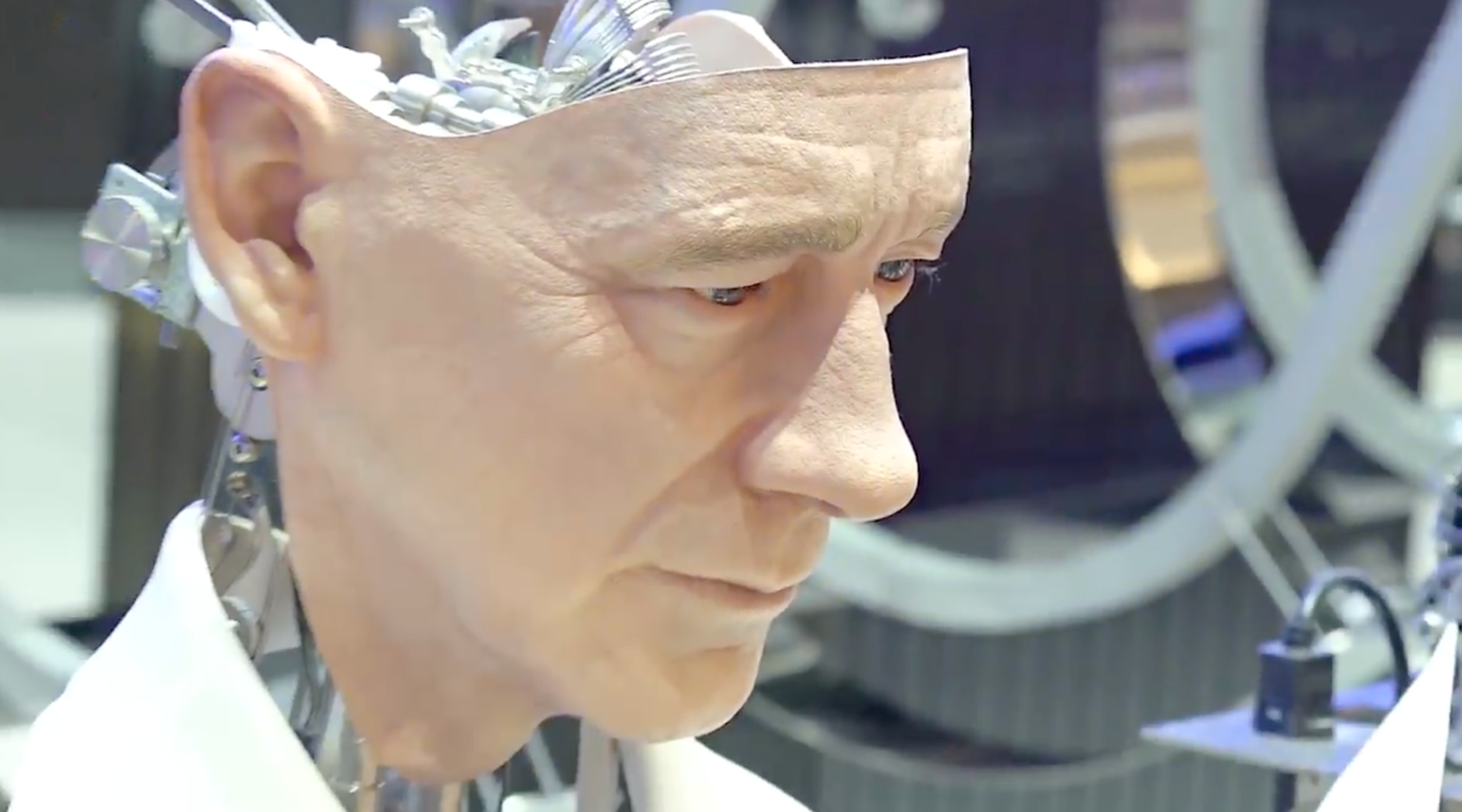
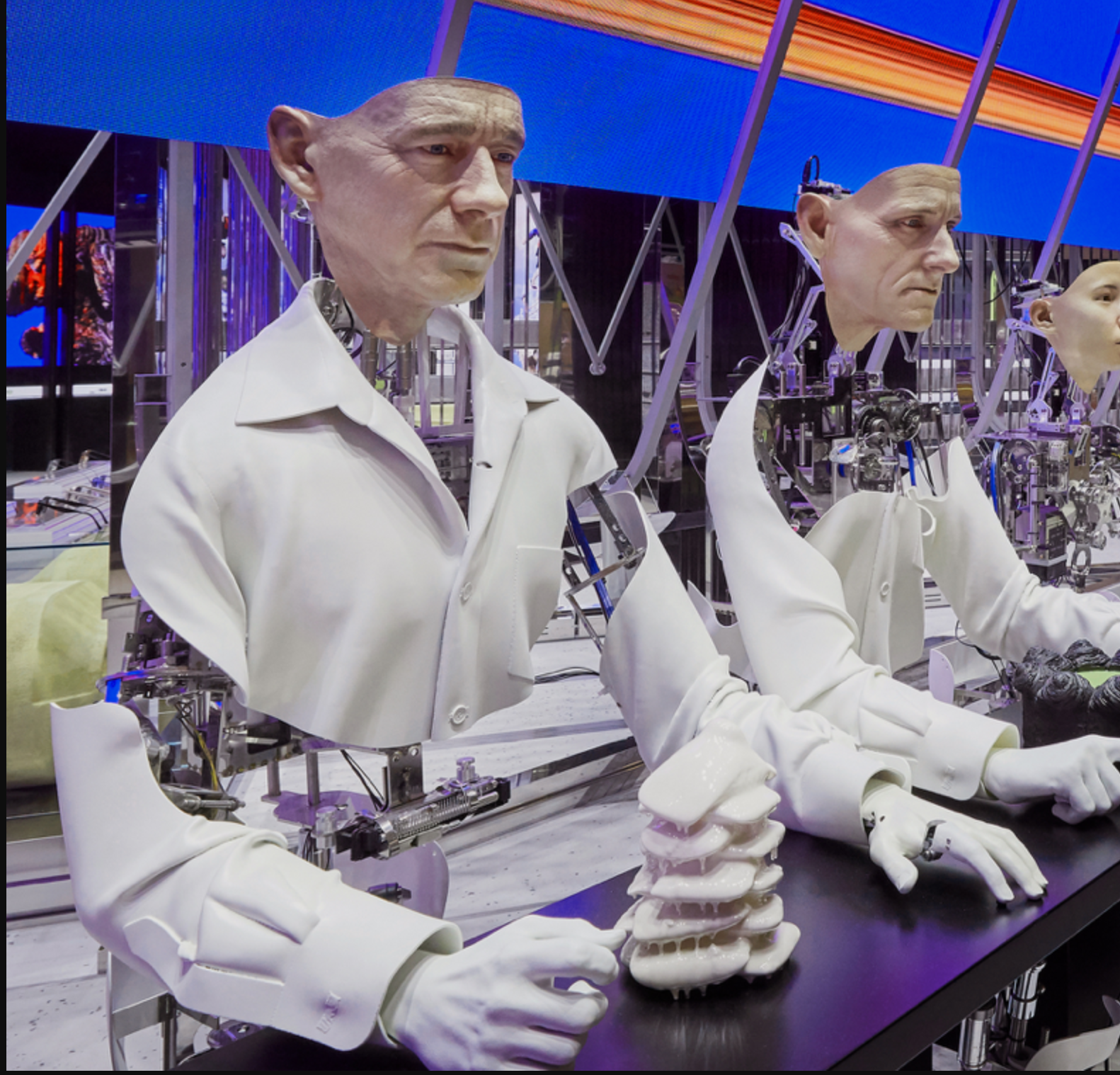
Time to hit the road and head to the airport (if I can find the car's keys!). The next destination is Seattle, and then back to the BOT island!
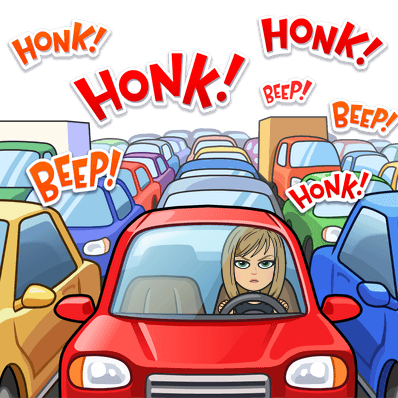
Korea, you are a beautiful country, and you have amazing people. Including the lady that saved me from taking the wrong connection TWICE!!
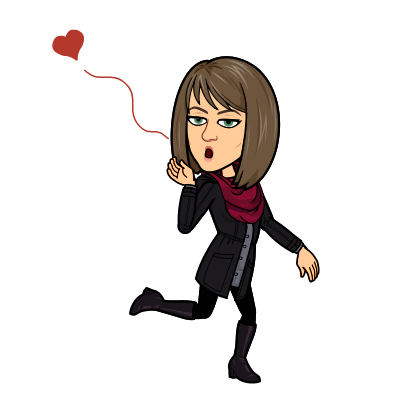